
Research & Initiatives
The fundamental research and transformative technology we’re developing and demonstrating will help solving the global challenges of our changing climate, growing clean energy demand and evolving energy markets. Together we will shape a better tomorrow.
The fundamental principles of thermal-fluid sciences can be found in various of engineering applications ranging from large-scale power plants energy generation to small-scale micro devices cooling, from HVAC systems in buildings, vehicles and space stations to natural phenomena. Innovative and cost-effective implementation of these technologies requires in-depth understanding of the underling physics involved in the mass and heat transfer processes.
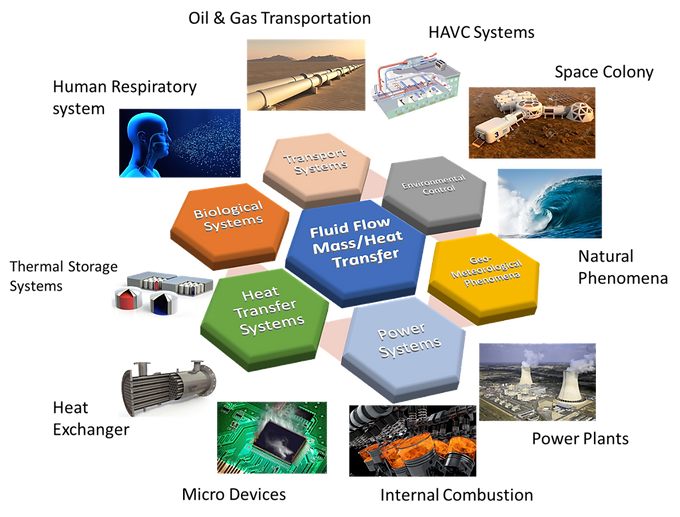
In AFHTL, based on the advanced high-resolution diagnose techniques, we're discovering new physics, advancing theoretical understanding, and developing state-of-the-art analysis tools that will accelerate the development and deployment of future clean energy systems.
Current Research Grants
-
Development of Innovative Physics‐Informed Data‐Driven Model for COBRA‐TF Critical Heat Flux Prediction in Support of Future Nuclear Energy Sustainability
MU Research Council Grant
Jan. 2023 - Present

-
Advanced Reflood Thermal-Hydraulics for Uncertainty Resolution (ARTHUR) Task Order No. 002: Reflood and Droplet Measurement at Low Flowrates Using Rod Bundle Heat Transfer (RBHT) Test Facility
Penn State Univ. / Nuclear Regulatory Commission
Feb. 2023 - Jan. 2024

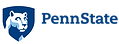
-
Midwest Industrial Assessment Center
Department of Energy
Nov. 2022 - Present

-
Address Thermal Hydraulic Issues Through Experiments in the Rod Bundle Heat Transfer (RBHT) Facility
Penn State Univ. / Nuclear Regulatory Commission
Sep. 2024 - Present

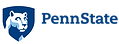
-
Massive Reflood Data Evaluation Using Machine Learning and Artificial Intelligence
Penn State Univ. / Nuclear Regulatory Commission
Sep. 2024 - Present

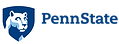
Research Projects
High-Resolution Experiments
Development of Computer Vision-Aided Image Processing Techniques for Flow Field Reconstruction



Numerical Simulation
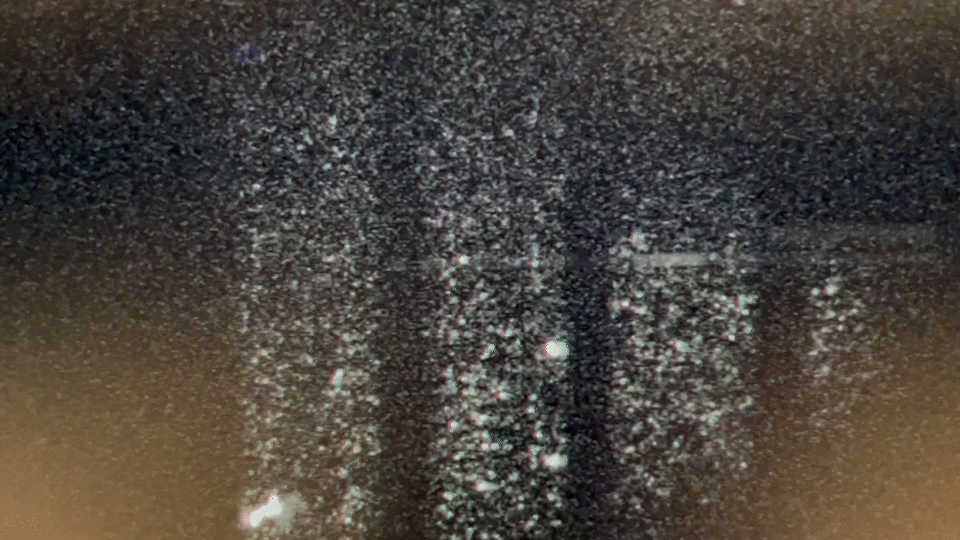
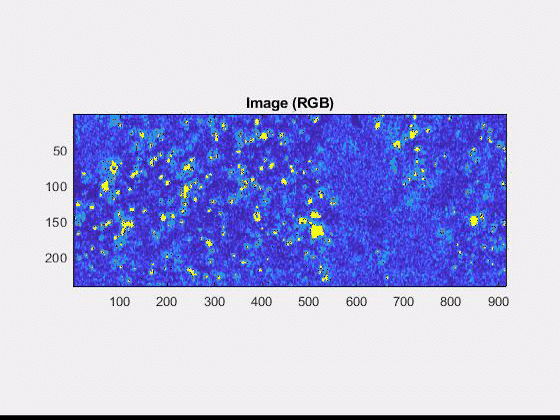
Raw PIV/LIF Images
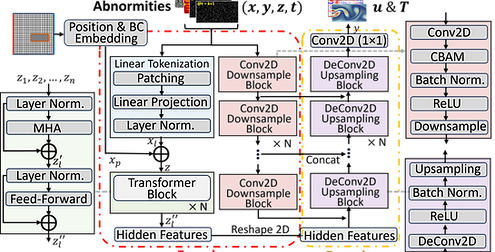
Image Processing
Many energy system safety related thermal hydraulic phenomena heavily depend on the local 3-D and micro-scale fluid dynamics and heat transfer processes. However, obtaining detailed information using conventional experimental and numerical techniques is extremely challenging. The objective of the proposed project seeks to develop a novel artificial intelligence (AI)-based image processing and modeling approach leveraging advanced flow visualization techniques in complex geometries. By utilizing Stereo-Particulate Imaging Velocity/Laser Induced Fluorescence (S-PIV/LIF) and Infrared (IR) Thermal Imaging techniques, high-spatiotemporal-resolution flow and heat transfer data will be collected from the flow and heat transfer loop (FHTL) under varying system conditions and geometries. The imaging data obtained will be processed using advanced data visualization techniques to accurately extract full-field 3-component (3C) velocity and temperature distributions. Building on this, we will further leverage the state-of-the-art computer vision and machine learning (CV&ML) techniques to develop an ultra-fast data-driven predictive model capable of accurately characterizing the liquid-solid heat transfer behavior based solely on the flow information, regardless of varying geometries and conditions. After a thorough validation, the integration of CV&ML models with S-PIV/LIF techniques will enable the detailed analysis of local 3-D flow and heat transfer behaviors, thus not only exceeding existing 1-D analysis tools but also eliminating the reliance on costly and time-consuming CFD simulations.
Visualization of the two-phase flow interface behavior using advanced image processing techniques
Raw Images
Processed Images
In this study, based on a small-scale quench test facility, the two-phase flow interface behavior during quench transients is visualized and analyzed utilizing an image processing framework coupled with high-speed camera system. The high-fidelity experimental results obtained for two-phase flow in the current framework can support various studies both in the time domain and in the frequency domain. In particular, visualization of the data obtained from different heating surfaces under different test conditions are used to perform a full-scale transient 2-D vapor film reconstruction. The liquid-vapor interface variations in various heat transfer regimes as well as at the initial film breakup point can be directly obtained through the processed data. Moreover, the temporal variation of the interfacial wave frequency approaching quench is investigated in detail.
Visualization of the liquid droplets dynamics using laser imaging system during quench transients
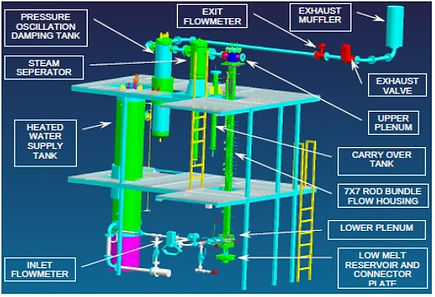
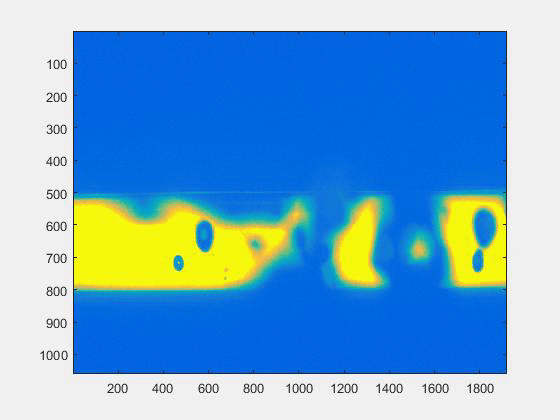

Non-intrusive laser imaging
NRC/PSU RBHT Test Facility
During reflood, the dispersed flow film boiling (DFFB) regime is expected to occur within the rod bundle assemblies. DFFB is generally characterized by dispersed liquid droplets entrained by the superheated vapor, which is the continuous phase. The mechanisms of cooling under reflood are complex and several heat transfer mechanisms occur, including laminar and turbulent convection between single-phase vapor and the rod surface, enhancement of heat transfer between liquid droplets and the superheated rod surface (dry wall contact), and radiation heat transfer from the rod to the steam, droplets and surrounding structure.
The major motivation for this study is to seek a better understanding of the droplet dynamics during reflood transients. The droplet sizes and distributions are investigated using the data obtained from the NRC/PSU RBHT test facility based on the Oxford Lasers Firefly Imaging Systems.
Theoretical Modeling
Similarity Solution of fine velocity and temperature distributions for two phases during natural-circulation film boiling
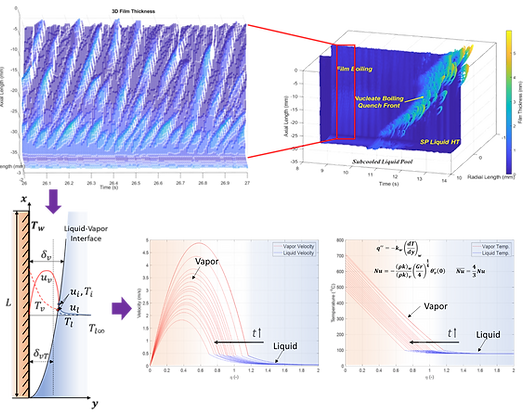
2-D liquid-vapor interface reconstruction
Similarity transformation in boundary layer
Based on the high-resolution data obtained for the liquid-vapor interface and a full scale interface reconstruction, the detailed phase velocity and temperature profiles are obtained through theoretic analysis in the boundary layer scale, based on which the film boiling heat transfer coefficient (HTC) can be determined. In addition, an improved film boiling HTC model is developed considering the effects of wall superheat, liquid subcooling temperature, vapor film thickness as well as fluid properties. The model is found to predict film boiling HTC well within 15% error.
Two-Phase flow drift velocity and mass quality modeling in the DFFB flow regime
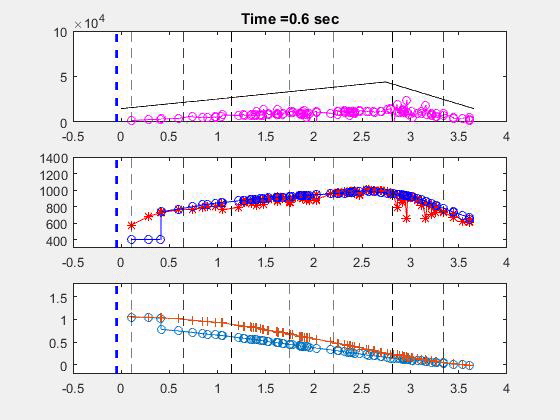
Heat Flux
Temperature
Quality
heating surface
vapor

A new semi-empirical two-phase flow mass quality correlation was developed for the post-dryout dispersed flow film boiling (DFFB) regime in a 7×7 rod bundle geometry. Starting from the fundamental physics describing the two-phase flow in the dispersed droplet flow regime, scaling analysis was performed within a sub-channel of the rod bundle to obtain an expression for the vapor drift velocity, from which a suitable relationship for the two-phase flow quality was derived using the drift flux model.
It was found that the vapor drift velocity in the DFFB regime is affected by many variables including: the droplet size, velocities of the liquid and vapor phases, void fraction, vapor superheat and fluid properties, all of which are important in characterizing the dispersed droplet flow. Based on the results of the RBHT reflood tests, a new mass quality correlation predicting two-phase flow mass quality was developed with significantly improved accuracy not only for the rod bundle geometry but also for the tube geometry
Modeling of droplets breakup over a heated strip in DFFB heat transfer regime
high-resolution laser imaging
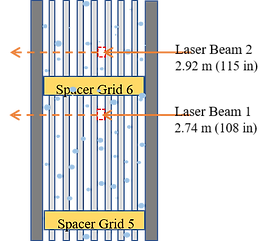
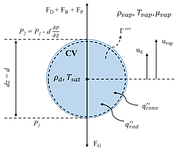
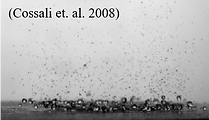

breakup process over strip
droplet and vapor dynamics
The interfacial heat and mass transfer process for the dispersed liquid droplets entrained in the continuous vapor phase has been the topic of scientific research for decades. Frequently, these liquid droplets would come in contact with the dry or wet heated surfaces at different angles. The ensuring droplet breakup, deposition or surface rewet may lead to significantly different heat and mass transfer behaviors. Such thermal-hydraulic transients involved in the two-phase flow system may be encountered in many engineering applications, for instance, in direct injection engines with spray cooling, or the droplet breakup during nuclear reactor reflood transients in a Loss Of Coolant Accident (LOCA). Other engineering systems where the liquid droplet entrainment can be frequently encountered include the cryogenic systems, steam generators, refrigeration systems, atomizers, etc.
In this work, the liquid droplet breakup process at the leading edge of a dry spacer grid during is studied theoretically based on the experimental observations using laser imaging system.
Constructing innovative CHF model based on the physics-informed machine learning methodology
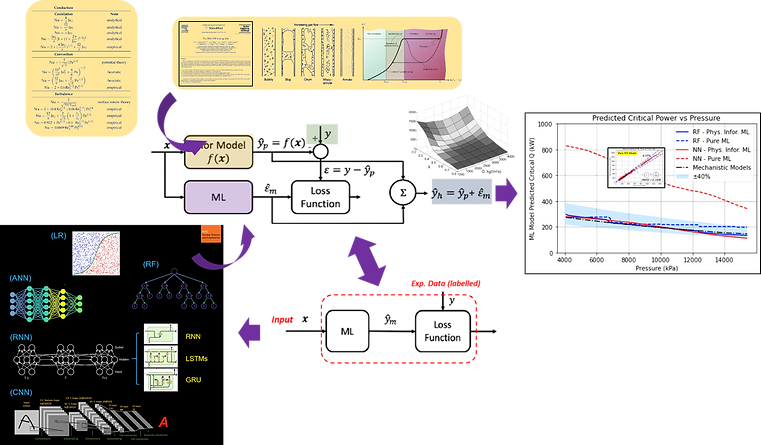
Machine learning structures
CHF prediction
Physics models
Accurate prediction of CHF under various fluid flow conditions continues to be required for design, operation and safety analysis of light water reactor rod bundles. Due to the lack of in-depth physical understanding as well as limited high-resolution data in the micro-scale flow and heat transfer, the existing models feature a sub-optimal uncertainty band. In this study, driven by the prior domain knowledge information obtained, an improved CHF look-up table is developed through unified AI-based machine learning algorithms for the vertical flow conditions within tube and annulus geometry. The Groeneveld 2006 look-up table is used as the domain knowledge to train machine learning process against tube and annulus CHF data for both DNB and DO type. The new look-up table shows improved accuracy for conditions relevant to PWRs and BWRs. In addition, its domain knowledge informed nature ensures that a rationale prediction can be made, thus accounting for previous valuable information in the machine learning model training process.
Advanced Numerical Modeling and Simulation
Assessment of coated cladding impact on nuclear fuel performance during plant design basis accidents
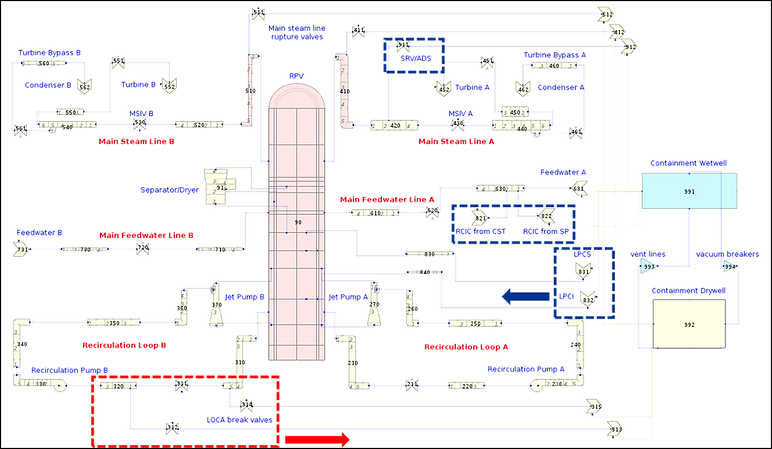
Boiling water reactor system model
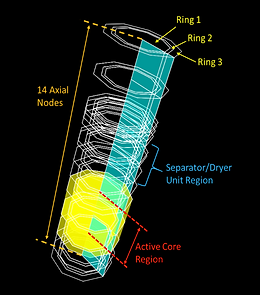
Reactor core modeling
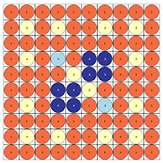
Nuclear fuel assembly modeling


Coated Zr fuel cladding
Since 2011, the U.S. Department of Energy has launched new research and development (R&D) programs for developing new accident tolerant fuels (ATFs) for nuclear power plants. These new fuel concepts are expected to bring several advancements in terms of plant safety. However, development, licensing, as well as deployment of ATF require a substantial investment among fuel vendors, operating utilities, and regulatory authorities. For ATF to be economically feasible, credited safety benefits may be necessary to provide an economic incentive for transition of nuclear power plants from Zr/UO2-based fuel technologies to ATFs.
Sensitivity analysis and uncertainty quantification for key safety quantities under LB-LOCA are performed for the Peach Bottom boiling water reactor (BWR) with GE-14 nuclear fuel design adopting the ATF concepts. A coupled TRACE-DAKOTA system analysis framework is developed to perform the uncertainty quantification.
Numerical investigation of quench transients in 7 X 7 rod bundle using sub-channel analysis tool

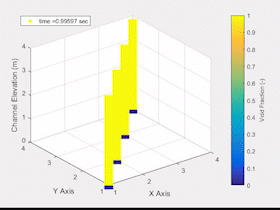
Flow Channel Void Fraction
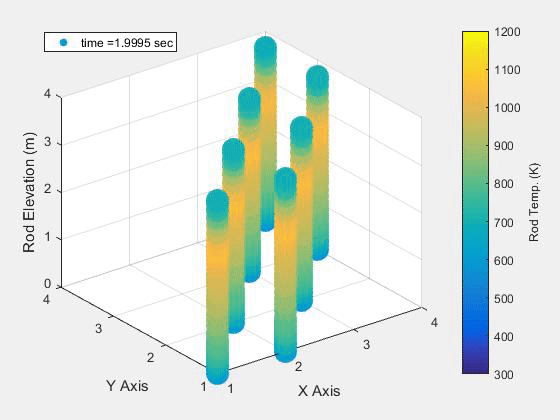
COBRA-TF Predicted Quench
Accurate prediction of the reflood transients during LOCA has long been a challenging task. One reason is the substantial cost incurred to perform large-scale reflood tests, which are formidable in experimental expenditure and intensive in technology as well as program management. Another reason preventing a comprehensive understanding of reflood transients is the high-level complexity involved in the two-phase flow mass and heat transfer processes, which makes the measurement extremely difficult and inefficient.
The situation has been significantly improved with the design and operation of the Nuclear Regulatory Commission (NRC)/Pennsylvania State University (PSU) Rod Bundle Heat Transfer (RBHT) test facility. A variety of advanced instrumentations were developed and used at this facility and very high-resolution data has been obtained, especially for the liquid droplet field. In the current study taking advantage of the unique NRC/PSU RBHT data, an extensive and comprehensive code evaluation and validation is carried out using the thermal-hydraulic sub-channel analysis code COBRA-TF. The present study clarifies the effect of different system parameters on the various two-phase flow quantities during reflood. The results obtained provide answers for many existing code modeling issues and thus can be instructive and useful for future model development and code upgrading.
Helium-Cooled FMR Upper Plenum Turbulent Mixing and Heat Transfer using CFD
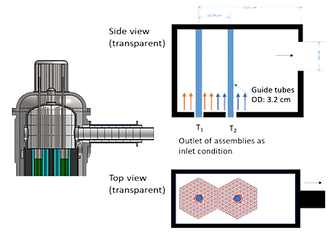
Helium-cooled 50 MWe Fast Modular Reactor
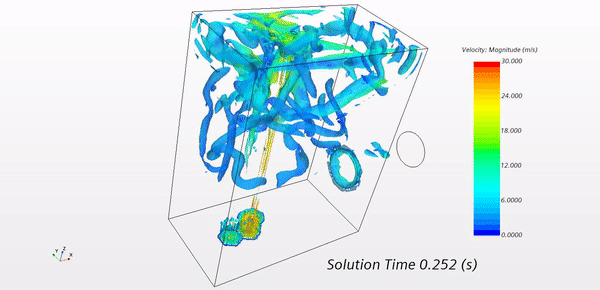
Turbulent Mixing Simulation

Fuel assembly Inlet conditions
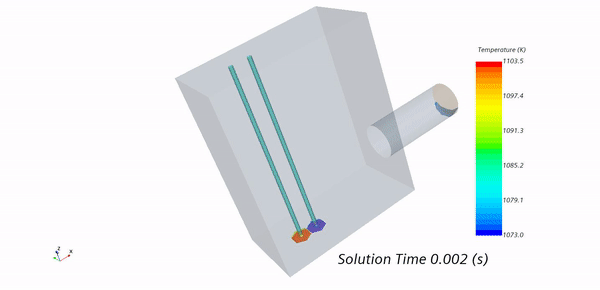
Thermal Striping
To support the development of advanced nuclear systems, accurate yet computationally affordable turbulence modeling option for thermal-striping predictions are of crucial importance. The design of upper internal structures, as well as lower plena and heat exchanger configuration, are strongly affected by the ability to efficiently mix the coolant streams and further affects the material selection as well as operation and maintenance of the systems. This study, as part of on-going NEUP-IRP project (Challenge Problem (CP) 2: Benchmark Specifications for Thermal Striping of Reactor Internals), generalizes specific needs related to the General Atomics Fast Modular Reactor (FMR) upper plenum designs by developing, demonstrating and quantifying the accuracy of the thermal striping modeling approach.
In this challenge problem we seek to develop an accurate and affordable turbulence modeling option for thermal striping predictions using a hybrid turbulence model. Thermal striping is inherently transient and therefore steady-state RANS has limited applicability. Historically, Large Eddy simulation (LES) was considered necessary to achieve good results in general configurations. However, due to its requirement for large computational resources, judicious selection of modeling approach including meshing technique is essential.
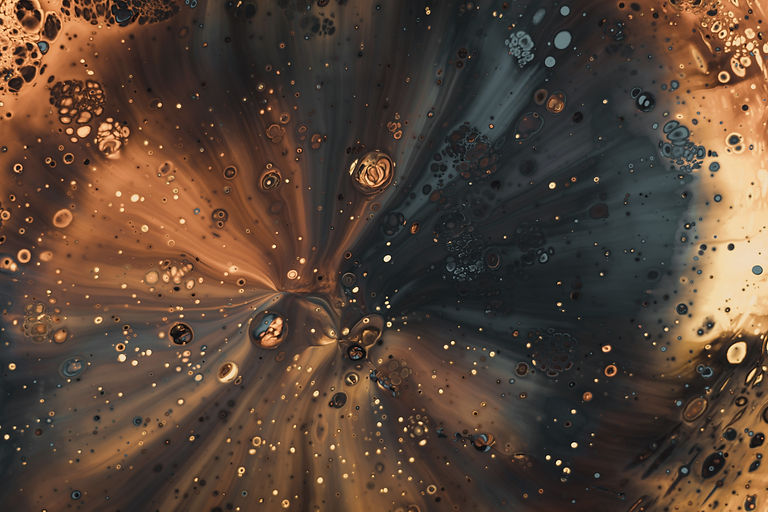